Understanding Die Casting Components: A Comprehensive Guide
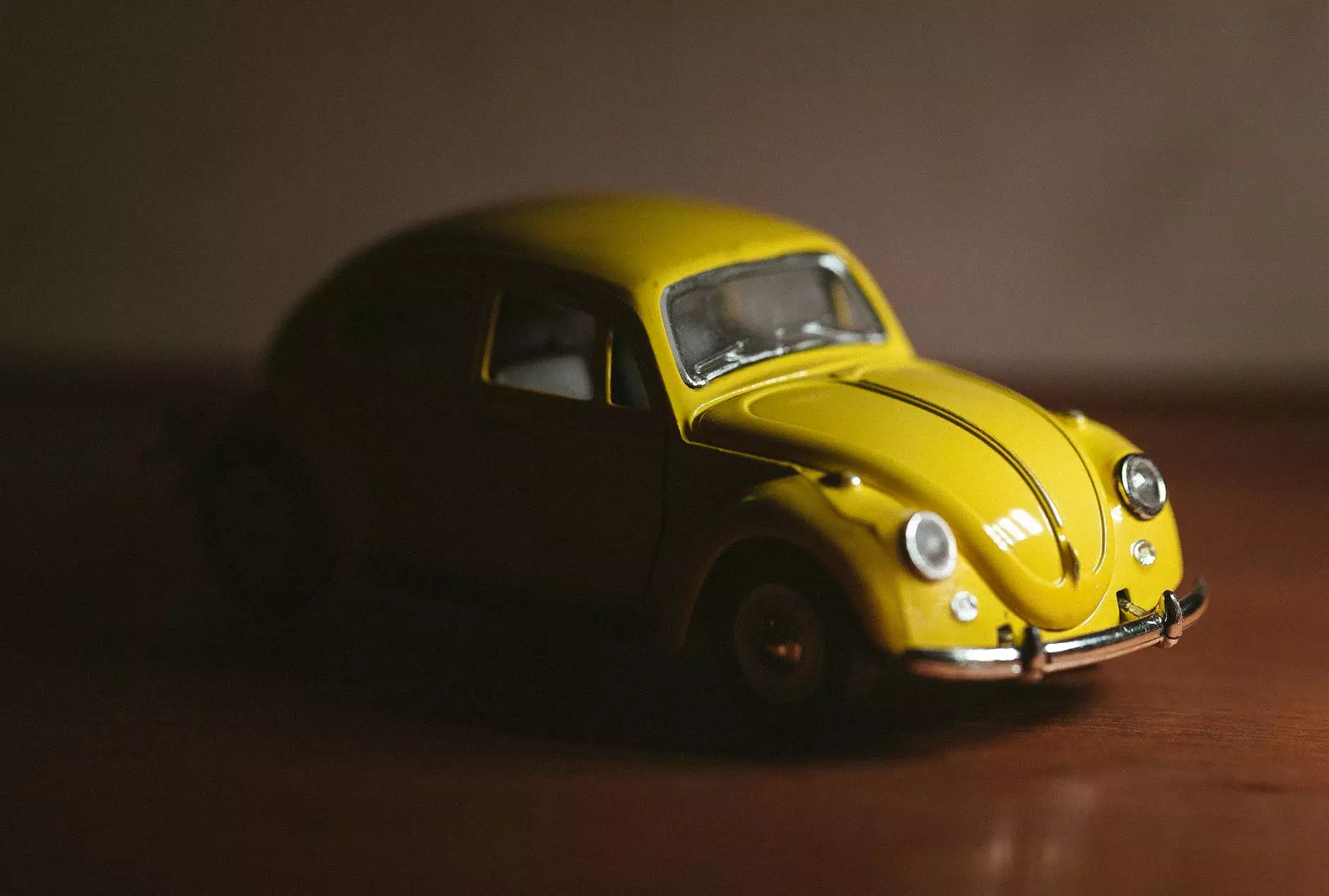
In the realm of manufacturing, die casting components hold a significant position due to their efficiency, precision, and versatility. Die casting is a metal casting process characterized by forcing molten metal under high pressure into a mold cavity. This article delves into what die casting components are, the die casting process, applications, advantages, and why choosing a top-notch provider like DeepMould.net is crucial for your business.
What Are Die Casting Components?
Die casting components are the parts created from the die casting process using various metals, particularly non-ferrous metals such as aluminum, magnesium, and zinc. These components are used across numerous industries including automotive, aerospace, electronics, and consumer goods. Their unique properties such as corrosion resistance, ductility, and high strength make them ideal for many applications.
The Die Casting Process
The die casting process consists of several critical steps that ensure high-quality end products. Understanding these steps provides insight into why die casting components are engineered for excellence.
1. Mold Preparation
The first step involves creating a mold that consists of two parts: the cover mold and the ejector mold. High-quality molds are crucial as they define the shape and dimensions of the components.
2. Melting the Metal
Next, metal is melted in a furnace at a temperature specific to the metal type. It is essential that the metal reaches an optimal temperature to ensure a smooth pour without defects.
3. Injecting the Molten Metal
Once the metal is molten, it is injected into the prepared mold using a hydraulic or mechanical press. This step is done at very high speed, ensuring the mold fills completely before it starts to solidify.
4. Cooling and Ejection
After the molten metal fills the mold, it is left to cool. This cooling process can take seconds or minutes depending on the thickness of the component. Once cooled, the mold opens, and the casting is ejected.
Benefits of Die Casting Components
There are numerous advantages to utilizing die casting components in manufacturing, which sets them apart from other fabrication methods:
- Cost-Effectiveness: Die casting allows for high-volume production, significantly reducing per-unit costs over time.
- Precision and Accuracy: The high-pressure injection of molten metal results in components with tight tolerances and minimal finishing required.
- Complex Shapes: Die casting can produce intricate shapes that are difficult to achieve with other processes.
- Surface Finish: Components produced have a smooth surface finish that often requires little to no post-processing.
- Variety of Materials: A range of non-ferrous metals can be used, including aluminum, zinc, and magnesium, offering various properties suited for specific applications.
Applications of Die Casting Components
The versatility of die casting components makes them suitable for various industries:
1. Automotive Industry
Die casting is extensively used in the automotive sector for parts like engine blocks, transmission housings, and brackets. The lightweight nature of aluminum die castings helps in enhancing fuel efficiency.
2. Aerospace Industry
In aerospace, die casting components are crucial due to their strength-to-weight ratio. Components such as landing gear parts and structural elements are manufactured through die casting for reliability and performance.
3. Electronics and Electrical Components
Die casting is also used in the electronics industry for creating housing for various devices, heat sinks, and connectors which require both durability and good thermal conductivity.
4. Consumer Goods
Products like appliances, furniture hardware, and decorative items also benefit from die casting, providing aesthetic appeal along with functionality.
The Importance of Choosing the Right Manufacturer
When sourcing die casting components, the choice of manufacturer can significantly influence the quality and performance of the final products. DeepMould.net stands out as a leading provider committed to excellence and customer satisfaction. Here’s why:
1. Quality Assurance
DeepMould.net implements stringent quality control measures at every stage of the die casting process to ensure that only the highest quality components are delivered to clients.
2. Advanced Technology
Utilizing the latest technologies and equipment, DeepMould.net can produce complex die casting components with precision that meets the most demanding specifications.
3. Custom Solutions
The company offers customized solutions tailored to meet the specific needs of clients, ensuring that each component is fit for its intended application.
4. Fast Turnaround Times
With streamlined processes and efficient production capabilities, DeepMould.net provides quick turnaround times, allowing businesses to meet deadlines without compromising on quality.
Case Studies: Success Stories from DeepMould.net
1. Automotive Engine Components
A major automotive manufacturer faced challenges with the weight and performance of their engine components. By switching to high-quality aluminum die casting components from DeepMould.net, they achieved a significant reduction in weight while enhancing performance and fuel efficiency.
2. Aerospace Structural Parts
In another instance, an aerospace company required precisely engineered structural components that could withstand extreme conditions. DeepMould.net delivered custom die casting solutions that passed rigorous testing, showcasing reliability and durability in critical applications.
Conclusion
Die casting components are invaluable in modern manufacturing, offering a blend of efficiency, cost-effectiveness, and high-quality production. Understanding the die casting process, its benefits, and applications can help businesses make informed decisions. Trusting experts like DeepMould.net for your die casting needs ensures that you receive components that not only meet but exceed industry standards, positioning your business for success in a competitive landscape.
For more information on die casting components or to discuss your project requirements, visit DeepMould.net today!