CNC Lathed Parts: A Comprehensive Guide to Quality and Innovation in Metal Fabrication
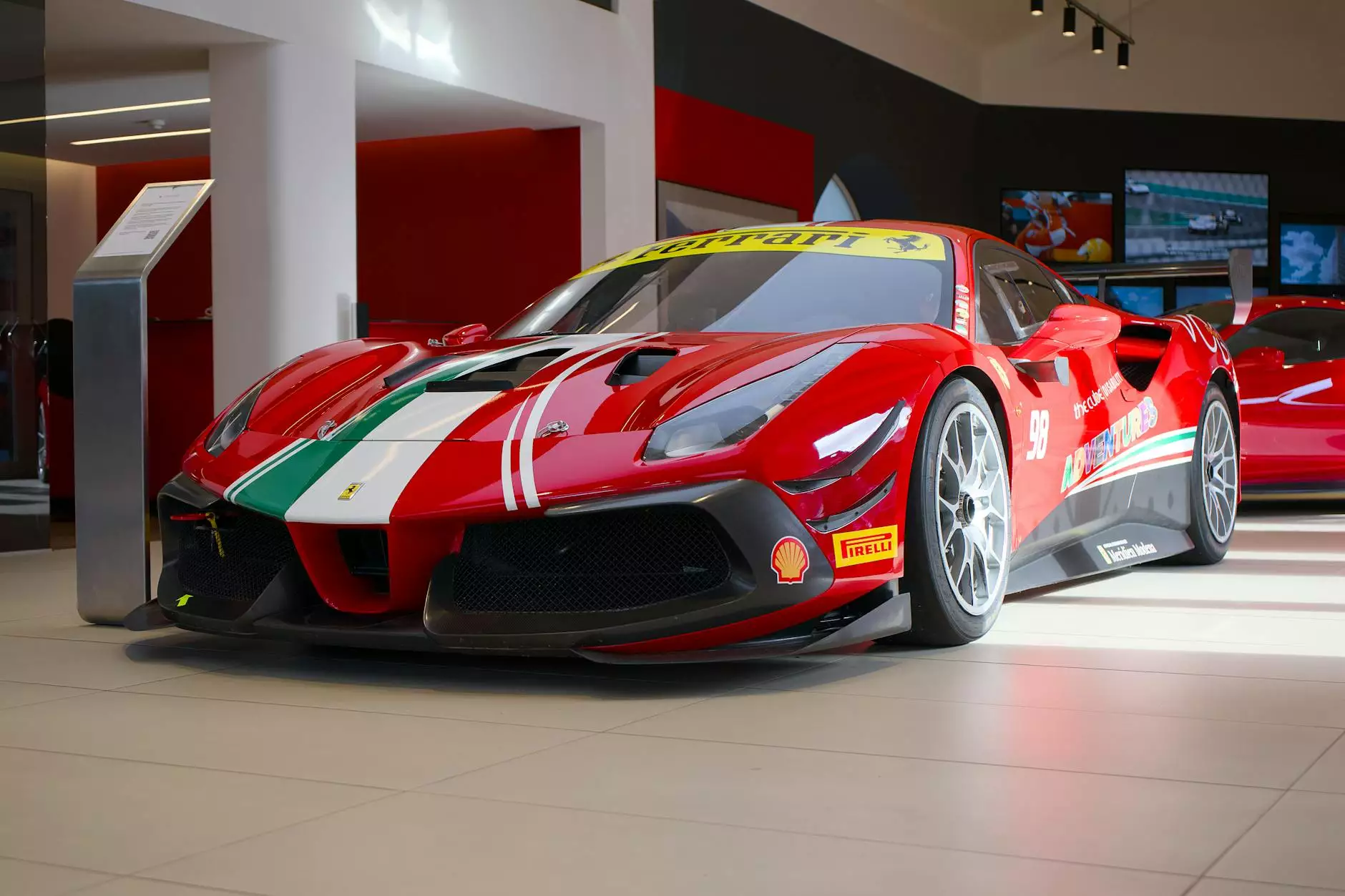
In today's manufacturing landscape, precision and accuracy are paramount. CNC lathed parts have revolutionized the way we approach metal fabrication. From industries ranging from automotive to aerospace, CNC (Computer Numerical Control) turning has become an essential process offering remarkable benefits. In this article, we will delve deep into the world of CNC lathed parts, providing you with insights into their importance, processes involved, and considerations for choosing the right manufacturer.
Understanding CNC Lathed Parts
CNC lathed parts are components produced using a CNC lathe machine, which allows for the precise rotation of metal pieces while various cutting tools remove material to form the desired shape. The process is known for its unparalleled accuracy, repeatability, and efficiency, making it a preferred choice in modern manufacturing.
The CNC Machining Process
At the core of producing CNC lathed parts is the machining process itself. Here’s a detailed breakdown of how CNC machining works:
- Design Phase: Initially, engineers and designers create a detailed blueprint or a 3D model of the part using CAD (Computer-Aided Design) software.
- CNC Programming: The CAD model is then transformed into a set of instructions, often using a CAM (Computer-Aided Manufacturing) system. This programming tells the CNC machine how to move, what speed to operate, and which tools to use.
- Setup: The CNC lathe is set up with the required tools, and the metal stock is secured in place.
- Manufacturing: The CNC machine automates the cutting process, precisely shaping the material according to the provided instructions.
- Finishing: After machining, parts may require additional finishing processes such as polishing, anodizing, or plating to meet specific tolerances and surface finishes.
Applications of CNC Lathed Parts
CNC lathed parts are ubiquitous across various industries due to their versatility. Here are some notable applications:
- Automotive: Components such as axles, shafts, and brackets.
- Aerospace: Precision parts required for aircraft assemblies, including landing gear and engine mounts.
- Medical Devices: Surgical tools and implants that demand high precision and durability.
- Electronics: Housings and connectors for electronic devices.
- Oil and Gas: Valve components and fittings that must withstand harsh environments.
Benefits of Using CNC Lathed Parts
The advantages of employing CNC lathed parts in production are significant:
- Precision: CNC machining can achieve tolerances as tight as ±0.005 mm, ensuring parts fit perfectly within assemblies.
- Efficiency: Automated processes reduce manual labor and increase production speed.
- Reproducibility: Once a design has been programmed, identical parts can be produced with no variation.
- Material Versatility: CNC lathes can work with a wide range of materials such as metals, plastics, and composites.
- Cost-Effective: While initial setup may be costly, the savings from reduced labor, waste, and increased production speeds can offset these costs significantly.
Choosing the Right Manufacturer for CNC Lathed Parts
When it comes to sourcing CNC lathed parts, selecting a reputable manufacturer is crucial. Here are some key considerations:
1. Experience and Expertise
Check the manufacturer’s experience in producing CNC lathed parts. A company with a proven track record, like DeepMould.net, often indicates reliability and quality.
2. Technology and Equipment
The quality of the CNC machines and tools makes a significant difference. Advanced technologies like multi-axis lathes can enhance precision and allow for complex shapes.
3. Quality Control Processes
Inquire about their quality assurance measures. A good manufacturer will have strict quality control processes to ensure all products meet specified tolerances.
4. Material Options
Look for manufacturers that offer a variety of material options to ensure that your components are made from the most appropriate materials for your application.
5. Capabilities and Capacity
Ensure that the manufacturer can handle your order volume and has the capability to scale production if your needs change.
6. Communication and Customer Service
Effective communication is key to a successful partnership. Choose a manufacturer that prioritizes customer service and provides clear communication at every stage of the process.
Trends in CNC Lathed Parts Production
The landscape of CNC machining is continuously evolving. Here are a few trends shaping the future of CNC lathed parts production:
1. Automation and Industry 4.0
With the advancement of Industry 4.0, manufacturers are increasingly integrating artificial intelligence and machine learning into CNC processes. This allows for more efficient operations, reduced downtime, and predictive maintenance.
2. Sustainable Manufacturing
As industries shift towards sustainability, manufacturers are adopting eco-friendly practices such as using biodegradable cutting fluids and recycling waste materials. This not only helps the environment but can also enhance brand reputation.
3. Customization and Prototyping
Customers increasingly seek customized solutions. CNC lathed parts allow for rapid prototyping and customization, enabling businesses to quickly adapt to market changes.
4. Integrated Supply Chains
Manufacturers are increasingly integrating their supply chains to increase efficiency and reduce lead times. This trend ensures that all components are delivered on time and meet the necessary specifications.
Conclusion
In conclusion, CNC lathed parts are crucial in modern manufacturing, offering precision, efficiency, and versatility across various industries. By understanding the various processes, applications, and considerations for choosing manufacturers like DeepMould.net, businesses can optimize their fabrication processes and achieve high-quality outcomes. As the industry evolves, staying informed about trends such as automation and sustainability will further enable companies to leverage the full potential of CNC lathed parts.
Emphasizing quality and innovation in your manufacturing processes is no longer optional—it’s a necessity for staying competitive. Invest in CNC lathed parts and take your production capabilities to the next level.