Exploring the Benefits and Applications of Die Casting Products
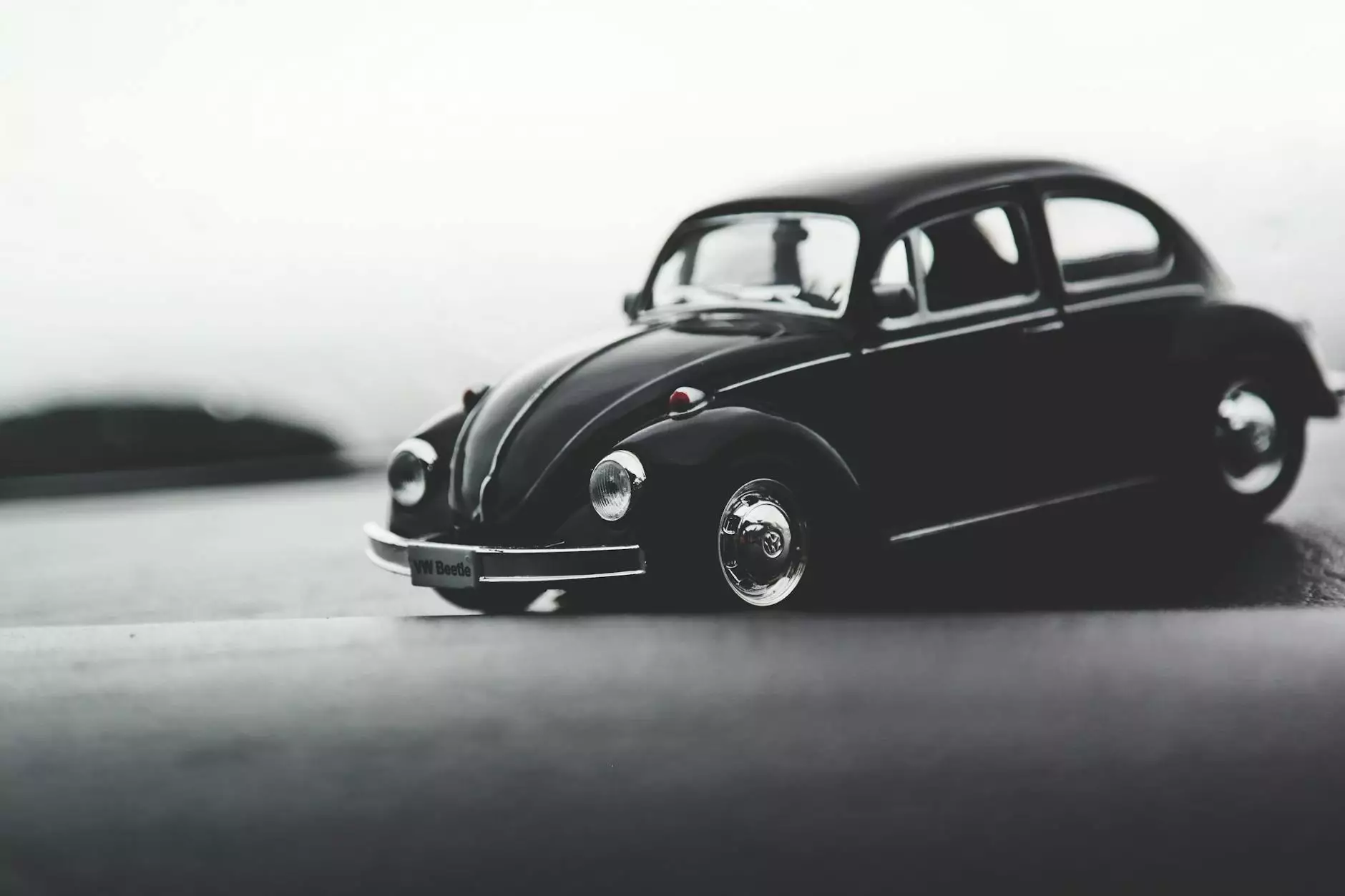
Die casting products represent a vital segment in the world of manufacturing, renowned for their precision, durability, and cost-effectiveness. As industries evolve, the relevance of die casting continues to grow, providing an array of benefits for manufacturers and consumers alike.
The Fundamentals of Die Casting
Die casting is a metal casting process that involves forcing molten metal under high pressure into a mold cavity. The molds, also known as dies, are precisely crafted to produce parts with exceptional detail and dimensional accuracy. Commonly used metals include aluminum, zinc, and magnesium, which offer unique properties suited for various applications.
Advantages of Die Casting Products
The advantages of using die casting products are manifold:
- High Precision and Consistency: Die casting allows for consistent production of intricate parts with tight tolerances, making it ideal for high-volume applications.
- Diverse Material Options: A wide range of metals can be used in die casting, providing manufacturers with flexibility to choose materials based on specific requirements.
- Cost-Effectiveness: Despite the initial investment in dies, die casting often reduces production costs over time due to its efficiency in mass production.
- Enhanced Surface Quality: Die cast parts have a smooth surface finish, which often requires minimal post-processing.
- Strength and Durability: The mechanical properties of die cast metals ensure that products are resistant to wear and tear, making them suitable for demanding applications.
Applications of Die Casting Products
Die casting products are utilized across diverse industries, including:
1. Automotive Industry
The automotive sector is one of the largest consumers of die casting products. Companies rely on these components for:
- Engine Components: Many engine parts, such as cylinder heads and engine blocks, are manufactured using die casting due to their strength and lightweight characteristics.
- Transmission Housings: Die cast materials provide the necessary durability required for housing in vehicles, enabling longevity and performance.
- Body and Trim Parts: From brackets to decorative elements, die casting is widely used for producing detailed parts.
2. Electronics Industry
Die casting plays a crucial role in the production of electronic enclosures and components, where precision and reliability are paramount. Applications include:
- Heat Sinks: Effective thermal management in electronics is achieved through die cast heat sinks, ensuring prolonged component lifespan.
- Connectors and Housings: Accurate die cast parts are essential for electrical connectors, where misfits can lead to connectivity issues.
3. Aerospace Sector
The aerospace industry also benefits from die casting products, which are used for:
- Structural Components: Lightweight yet strong components are critical for aircraft, making die casting ideal due to its material properties.
- Instrumentation Parts: Precision is vital for instruments in aviation, where die casting ensures operational accuracy.
Trends in Die Casting Products
The future of die casting is influenced by several emerging trends:
- Automation and Robotics: Increasing automation in die casting processes enhances production efficiency and reduces labor costs.
- Sustainability Practices: The incorporation of recycling practices and energy-efficient technologies is becoming a priority in die casting.
- Advanced Alloys: Research into new alloys is paving the way for even more durable and lighter die cast products.
The Process of Die Casting Explained
Understanding the die casting process involves knowing its key stages:
- Preparation: The first step is preparing the die, which includes cleaning and applying a release agent.
- Melting: Metal is heated to its melting point in a furnace.
- Injection: The molten metal is injected into the die under high pressure.
- Cooling: Once filled, the mold is cooled, allowing the metal to solidify.
- Ejection: The completed part is ejected from the die, and any excess material is trimmed.
- Finishing: Final surface treatment may be applied to enhance quality.
Quality Control in Die Casting
Ensuring the quality of die casting products is essential for performance and safety. Various techniques are employed:
- Dimensional Inspection: Measuring parts with precision tools to ensure they meet specifications.
- Visual Inspections: Conducting visual reviews for defects on the surface.
- Performance Testing: Subjecting parts to stress tests to validate durability and performance under operational conditions.
Conclusion: The Future of Die Casting Products
As industries continue to innovate, die casting products will remain a cornerstone in manufacturing. The blend of precision, versatility, and efficiency offered by die casting makes it an invaluable process in producing high-quality components across various sectors. With continued advancements in technology and materials, the future for die casting is not just promising but also pivotal in shaping the landscape of modern manufacturing.
For more information about die casting products and their applications, visit deepmould.net.